Its combination of energy efficiency, structural solidity,
resource conservation and low construction costs heralds a radical
change in the way homes and communities around the world can be
designed and built. With the ability to accommodate the ultimate in
creative expression due to it’s design flexibility. The construction
method does include such perks as tax breaks, generation of greenhouse
gas credits, reduced in insurance premiums and lower maintenance costs
an unlike other construction does not depreciate. The ultimate in
extreme weather housing, the insulation provided by the composite
materials is effective enough that the house can be heated or cooled
using less than half the energy it takes for a home built with
conventional materials. The foam / concrete house is more resistant to
fire, mold and pests than typical homes, and better able to withstand
such hazards as earthquakes, extreme weather, climate conditions and
flooding with it’s resistance to water. It natural resistance to pests
both insects and rodents reduce the costs associated with pest control,
exposure to toxic pesticides and the diseases transmitted by them. The
available non-porous interior designed without cracks and crevices
makes sterilization and cleaning a breeze. Complimented by the use of a
natural non-toxic residue free biocide, Anolyte solution, the same used
by the human body to destroy pathogens, created using salt water and
sunlight reduces the risk of contagions producing disease.
Compared to other environmentally sensitive, energy-efficient
construction methods this technique used for the foam house is better
by every measure. The method may have its greatest potential for a
significant impact in Third World nations. Foam / Concrete composite
buildings could be the answer to housing growing populations more
affordably, as well as more securely, particularly in regions
threatened by extreme climate chaos or prone to earthquakes. Optimized
for countries that do not have wood, steel, and other materials for
infrastructure, or which can be very expensive in those that do have
the resources. It can take months or up to three years to build just
one house, with this approach a house can go up in a matter of days.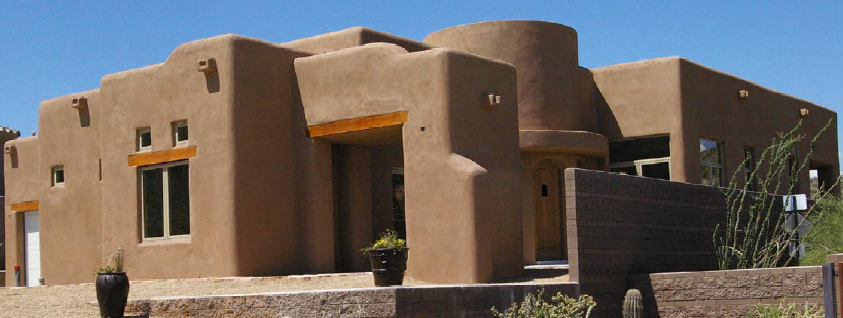
Test results also scored well in the Scottsdale Green Building program.
The components rated very high 80-points, indicating sustainability. In
terms of energy conservation, materials reduction, and other
environmental elements, it proved exceptionally earth friendly. The
buildings conserve raw materials by eliminating the need for
conventional structural components such as wood or metal framing,
straps, nails, wallboard, stucco, and insulation. The structures are
energy-efficient, with an energy rating of R40 in the walls and R100
for roofs. Typically found in homes, fiberglass blankets of insulation
have a nominal R-value rating of less than half of polystyrene foam.
Higher R-values translate into less energy consumption for heating and
cooling. It replaces every structural component, including walls,
floors, and roof, providing a near air-tight-building envelope.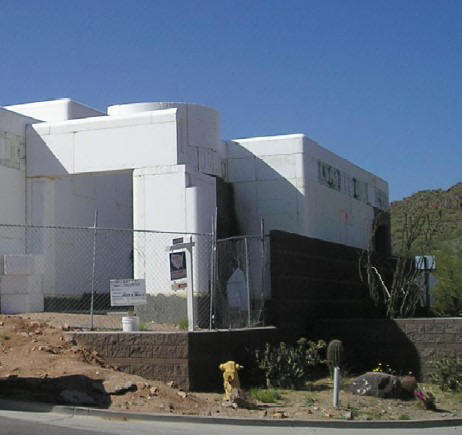
The new construction method and material is being targeted for use in
45 acre spiritual retreat, conference / workshop center, pod housing
and sustainable living prototype in New Mexico. One using surface soil remineralization in
place of petroleum based fertilizers and pesticides and Amaranth as a food
staple.
The new composite building system features a patented building
technique and material composed of expanded polystyrene foam coated
with a structurally reinforced concrete composite. These materials form
an incredibly strong bond to withstand building loads. Fibers are
disbursed throughout the matrix of the composite, which makes the
material three to five times stronger than steel. The foam cores are
over 98% air and provide the means to hold an outer concrete skin that
gives the structure its strength. When completed the structure is a
single seamless structure multiple components becoming one very solid
structure without cracks or crevices or structure weakening joints.
These bonded components are inexpensive to maintain, durable, and
resistant to fire, mold, pests, earthquakes and extreme weather and
wind conditions. The structure also provides superior insulating
qualities reducing the energy requirements for heating and cooling
combined with special ventilation the house is passive and sustainable
energy sources like wind, solar, and geothermal can easily meet all
energy requirements.
The structures can also be supplemented with additional technology to
provide shielding from electromagnetic radiation. The structure itself
can be turned into a large solar cell allowing for a distributed
decentralized energy infrastructure with each unit able to feed the
grid with surplus energy when equipped with battery storage. Each unit
is intelligently connected to a wireless mesh communications network
supported by each individual unit connected to all the rest as one
contiguous whole, for voice, data, and video. This allows hospitals and
manufacturing facilities to negotiate energy draws from each individual
unit providing fail safe distributed energy architecture.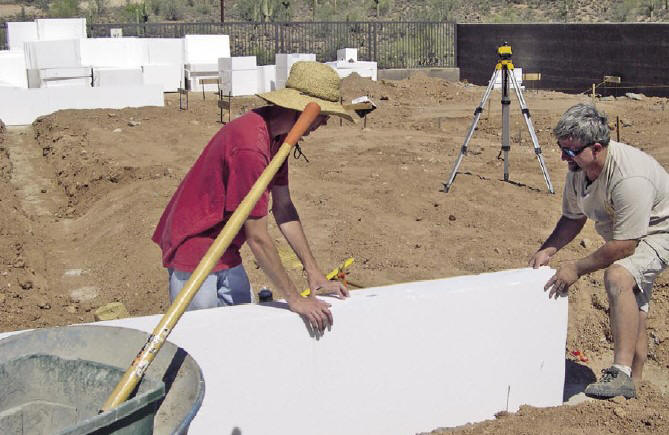
The technique binds the lightweight foam and a glass fiber-reinforced
concrete. Crucial to this method becoming viable is a special computer
program that takes an architectural design and slices it up into pieces
allowing the data to be fed to computer controlled foam cutters, which
produce the pieces for easy assembly. The light weight foam pieces
allow large panels to be lifted into place by a single worker.
The architects CAD/CAM design is processed generating digital
instructions that directed a robotic foam cutter to accurately carve
the polystyrene shapes required for the building. The end result is a
set of building blocks that may be curved, angular, or the more
traditional square and rectangular shapes. These individually fashioned
pieces are assembled onsite like LEGOs. The rectangular panels range up
to four by eight feet. Exterior walls are eight to ten inches thick,
and interior walls are four inches thick. Patented roof beams,
manufactured out of polystyrene foam and concrete composite, are
thirty-inch thick supports.
The box frame design is much stronger than conventional
construction. This increases the maximum span without requiring
internal supporting walls or posts. “Clear Span” construction provides
the designer free reign to use up to 40 feet of unobstructed space
between walls. After assembly with a special adhesive, the foam is
spray coated with cement creating a single one piece unit.
Special tools, such as nail guns, electric saws, or compressors, are
not necessary in the construction of a home. In actuality, the most
unusual machine needed during construction is a hotwire tool that is
used to cut out windows, doors, or other openings from the foam blocks.
Any mistakes are easily fixed with a handheld foam gun. It’s a
forgiving system that can be repaired easily with unskilled labor. A
worker can be taught to do the job in two or three days. And it is a
lot easier than wood frame construction.
The fusion of the foam and a glass fiber-reinforced concrete materials
offers enough strength and durability to construct a house without
using any standard framing or reinforcement — wood, steel or otherwise
— and without a single nail, bolt or screw. The result is a seamless
single piece structure limited in form only by the imagination the
design whether it be a conventional ranch, English Tudor, adobe or any
style that could be imagined including a house without right angles
having only curved surfaces. 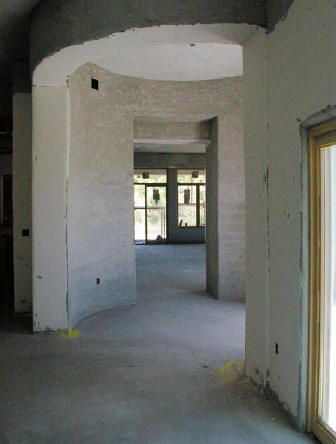
The other important achievement making this technology viable
is a patented method of predicting the performance of the structural
members of an entire building composed of these composites. Traditional
composite materials have had limited application in the building
industry because there have been no practical means for predicting the
performance of buildings using composites as structural members.
Desktop computing in the last few years advanced to the point where a
program could simulate the effects of earth movement, wind, snow load,
and other natural forces on these composite structures. The drawings of
the proposed building are used in concert with a mathematical program
called Finite Element Analysis. FEA is used to predict the performance
of the structure against the forces of nature. A performance record of
the building is available for review by architects, builders, and local
building authorities.
One major milestone and proof of viability was the passing of a series
of durability tests that conform to International Commercial Code (ICC)
standards. ICC requires a myriad of tests performed by an independent
laboratory for fire, aging, x-rays, water absorption, freeze/thaw, salt
spray, water penetration, seismic, and structural strength. it is clear
from the computer modeling that all aspects of structural concerns can
be met with this technology – wind, earthquakes, ground settling, etc.
which may become much more important in the near future with the threat
of Global Climate Chaos and extreme weather.
If the construction method is applied on a large scale, an
economy of scale is created resulting in costs well below those built
with conventional materials. Build time is very short, a few days,
which means a large number of units can be built and habitable within
weeks making it appropriate for rebuilding large areas ravaged by
extreme weather, earthquakes or other destructive forces.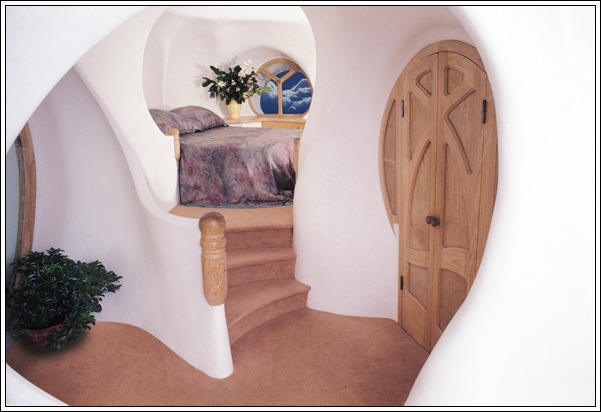
The walls consist of 8-inch-thick blocks of polystyrene coated with a
quarter inch thick "skin’ of the fiber concrete. The layer of concrete
is too thin to work just by itself and the foam is too weak to work by
itself. But when bonded together, the result is something to marvel at
perhaps qualifying as a miracle material.
The Composite, is poised to transform the construction industry by
being stronger, more design-flexible, less expensive and more
sustainable than conventional building materials and methods. It has
the potential to fundamentally change the way construction companies
conceive their projects, now that advanced computer age technologies
have caught up with the imagination of architects and builders to
create better and energy efficient structures. The composite introduces
21st century science, computer technology and mathematics to an
industry that still relies heavily on products and techniques
popularized in the 19th century and used ever since.
GOOGLE has provided a free 3D tool called SketchUp, which could enable
one to design a house online as only you can dream it. With assistance
from our architects your online design idea can become a reality, some
engineering guidelines and restrictions would apply. You could also
select from standard models and easily customize them and drag and drop
features, furniture and appliances etc.
1. Setting up
highly scalable manufacturing and R & D operations ramping up to
thousands
2. Design and
engineering aid
3. Site survey,
recommendations and feasibility process
4. CNC laser
EPS foam cutting operations mobile and base operations (tied into
bill of materials system, work order, MRP system, with bar coding and
RFID)
5. Structural
coating manufacture / mixing operation and storage.
6. Sequencing
Operation and System for delivery of all components to job sites based
on sales order and BOM. This would include the components of the
integrated technologies as well as electrical wiring harnesses and pre
cut plumbing if feasible.
7.
Documentation and certification
8. Online
configuration system with component and feature selection for customers
9. Local job
and skill training programs integrated with active projects.
Other
Integrated Sustainable Technologies
-
LED or
Plasma Lighting
-
Water
Collection & Storage
-
Geothermal
-
Solar
-
Wind
-
Heat
exchange controlled ventilation system
-
Battery
based energy storage
-
IP based
Wireless mesh communications (voice, video, internet data)
-
Anolyte
water purification and sterilization system
-
IP based
Smart House Control System
-
Smart
Electric Grid Interface
-
Epoxy
and Anti-Microbial Coatings
-
Water
and Flood Seal
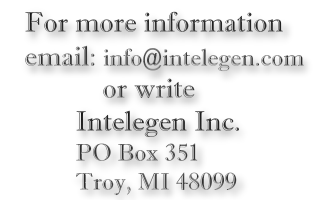
|